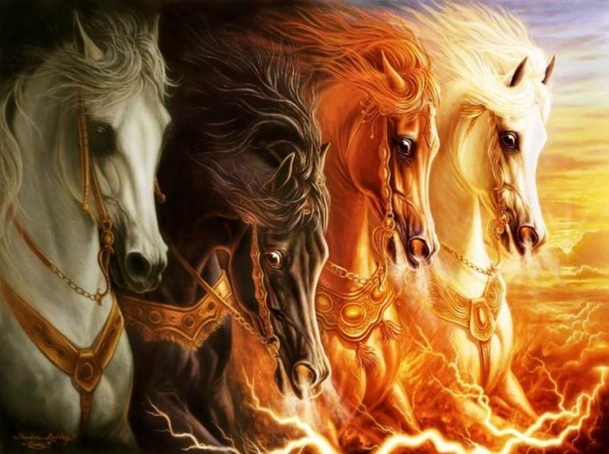
.
Так уж сложилось, что вся история становления цивилизации тесно связана с лошадьми. Эту удивительную связь можно проследить от самых сумрачных глубин осознанного развития человека до наших дней, поэтому сегодня мы с уверенностью можем утверждать, что лошадь всегда была верным помощником человека как в периоды созидания в повседневных трудах, так и в периоды разрушений во времена войн. Нам же это прекрасное животное послужит помощником в качестве аллегории для представления определенных технических решений, которые будут описаны в этой статье.
Из истории древнего Рима известны гонки на колесницах, которые запрягались четырьмя лошадьми — квадригах. Помимо боевой и спортивной функции квадриги в те времена выполняли еще и сакральную роль — римский триумфатор въезжал в город именно на такой колеснице. Сегодня квадриги можно увидеть на многих изображениях и барельефах, среди которых наиболее известные Бранденбургские ворота и Большой театр.
В те далекие времена человек, параллельно запрягая лошадей, увеличивал итоговую суммарная мощность, скорость и выносливость колесниц или повозок. Этот принцип только с параллельной установкой двигателей, сегодня нам известен в повседневной жизни, когда мы видим по несколько двигателей под крыльями самолетов гражданской, транспортной или военной авиации. Почему же не один, а несколько, ведь это усложняет управление? Да потому, что предел извлечения «положительных свойств из единицы» уже достигнут и повысить его невозможно, то есть нельзя одну лошадь заставить тянуть за четырех, или транспортный самолет взлететь на одном двигателе.
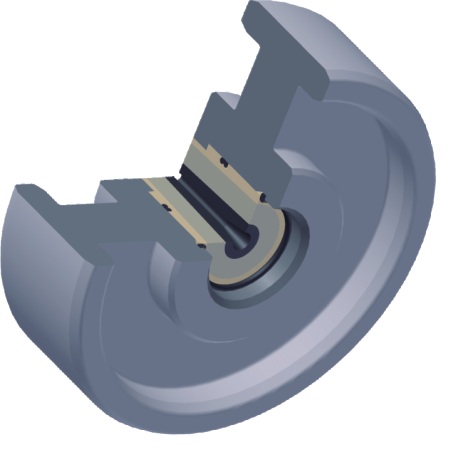
Чтобы лучше понять суть инновации сначала рассмотрим существующий уровень техники в области регулирования дебита скважин. Как известно в нефтегазодобыче все оборудование фонтанной арматуры работает в очень сложных условиях больших давлений и температур. Так пластовое давление при добыче углеводородов может достигать 800-900 кгс/см², температура на устье 135-150 °С и это при том, что дебит нефти достигает 3500 т/сут, газа- 1.5…2 млн. м³, более того в продукции скважины могут содержаться агрессивные составляющие: H2S — до 6% и CO2 — до 12% [1]. Основной удар тяжелых условий эксплуатации берут на себя детали запорной и регулирующей арматуры, при этом особенно быстро выходят из строя уплотнительные поверхности запорных органов. В результате теряется герметичность арматуры, привлекаются значительные материальные ресурсы для восстановления и поддержания работоспособности оборудования. В этих условиях для регулирования режима эксплуатации нефтяных или газовых скважин обычно применяются нерегулируемые или регулируемые дроссели (штуцеры). Более простыми и надежными являются нерегулируемые дроссели (Рис.1), которые обычно выполняется в виде диафрагмы с отверстием заданного диаметра, зажимаемой между двумя фланцами выкидной линии со скважины.
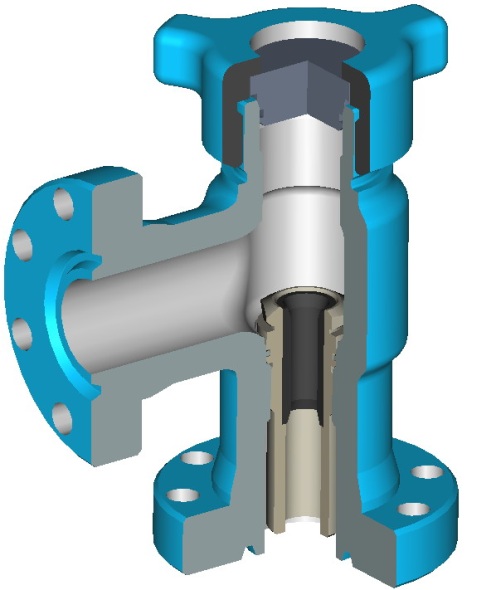
Но так как из скважины вместе с рабочей средой поступает песок или другой абразивный материал такие дроссели быстро выходят из строя. По мере «вымывания» отверстия в дросселе установленный режим работы скважины нарушается и его необходимо менять. Для этого работу скважины переводят временно на запасной отвод, на котором установлен резервный дроссель заданного диаметра, и одновременно меняют изношенный дроссель в основном рабочем отводе, таким образом, замена обычного дросселя трудоемка и длительна. Для облегчения и ускорения этой операции применяются дроссели с быстросъемными дроссельными втулками (Рис.2), которые при износе могут быть быстро сняты и заменены новыми.
Сменные дроссельные втулки обычно выполняются из легированной стали или из металлокерамического материала с центральным каналом заданного диаметра: 5, 8, 10, 15, 20, 25, 30 мм. Благодаря смене таких втулок можно ступенчато регулировать расход жидкости или газа. И хотя в этом случае не нужно разбирать фланцевое соединение, переключение на резервную линию и сброс давления с корпуса дросселя все так же необходимы, для чего требуется определенное время и определенные материальные затраты.
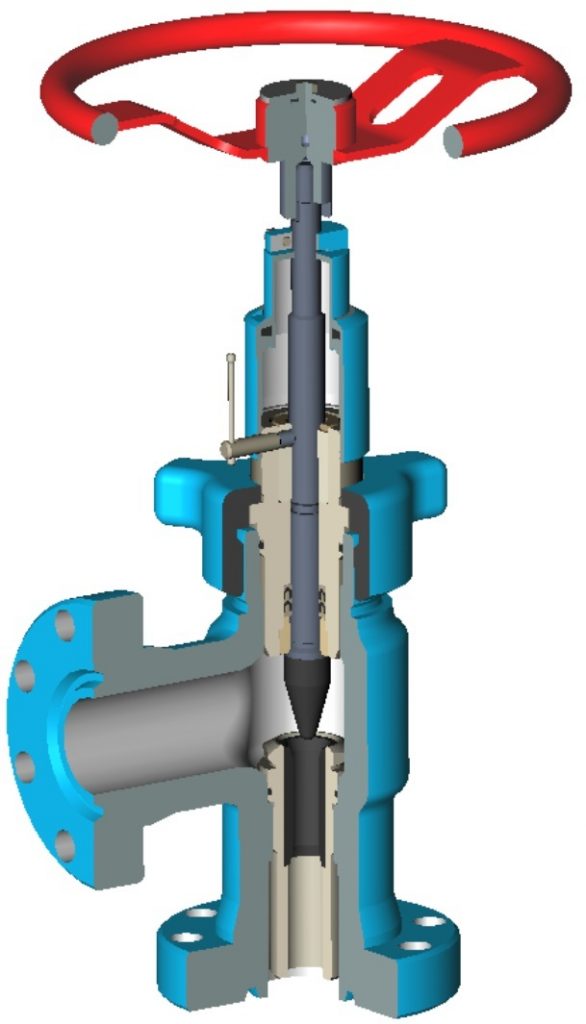
Для плавного регулирования режима эксплуатации скважины предназначен регулируемый угловой дроссель (Рис.3), который по конструкции аналогичен вентилю. Он позволяет бесступенчато регулировать давление на выходе фонтанной скважины за счет осевого перемещения шпинделя с насадкой, входящей в гнездо. Перемещение шпинделя осуществляется вращением маховика, на штоке которого имеется указатель, показывающий эквивалентный диаметр проходного кольцевого сечения регулируемого дросселя. Тем не менее, в агрессивных средах и при больших расходах загрязненной жидкости или газа в результате постоянного дросселирования насадка шпинделя и седло в корпусе быстро изнашиваются. Для повышения износостойкости этих деталей они изготовляются из специальных композитных материалов. Однако и это не исключает необходимости в частых ремонтах регулируемого дросселя, что является дорогостоящей операцией.
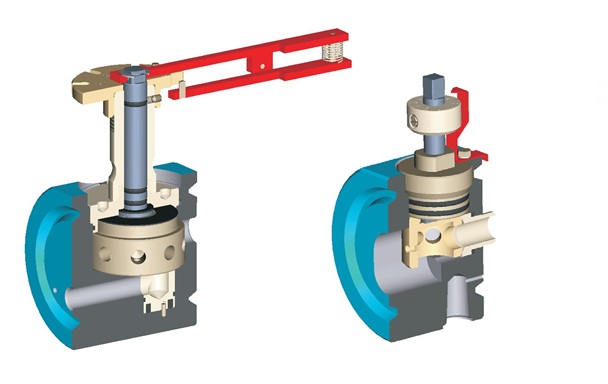
Сегодня заводы выпускают дискретные штуцерные дроссели (Рис.4), в которых изменение проходного сечения осуществляется простым поворотом цилиндрического золотника с отверстия различного диаметра и для чего, в отличие от нерегулируемых обычных дросселей, нет необходимости разбирать фланцевое соединение. К недостаткам данной конструкции относится невозможность восстановить изношенное отверстие, большие габариты и отсутствие возможности закрыть дроссель с обеспечением требуемой герметичности. Как альтернатива регулируемым дросселям встречаются еще и регулирующие клапана (Рис.5), но и у них регулирующие органы в связи с постоянным дросселированием рабочей среды быстро выходят из строя и клапан не может выполнять функции запорной арматуры.
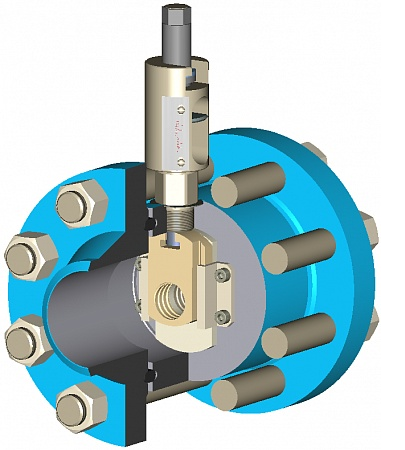
В последние годы на рынке можно встретить дисковые задвижки, которые оборудуются сменными дроссельными втулками и также используются для регулирования расхода. К преимуществам дисковых задвижек относят возможность переключения с помощью рукоятки и небольшие свободные внутренние объемы, что позволяет исключить замерзание рабочей среды в полостях при низких температурах. Сегодня есть два типа дисковых задвижек: дисковые штуцерные и дисковые револьверные. Конструкция у них практически идентичная.
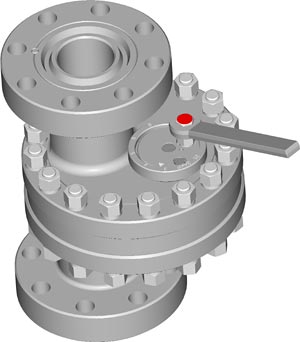
Дисковая револьверная задвижка (Рис.6) предназначена для ступенчатого регулирования расхода жидкости или газа за счет совмещения с патрубками несъемных дроссельных втулок различного диаметра, установленных в поворотном шибере. Принцип работы подобен, принципу работы описанного выше дискретного дросселя. Преимуществом конструкции является возможность закрыть задвижку с обеспечением класса герметичности А по ГОСТ 9544-2005. К недостаткам следует отнести невозможность заменить изношенную дроссельную втулку без разборки задвижки.
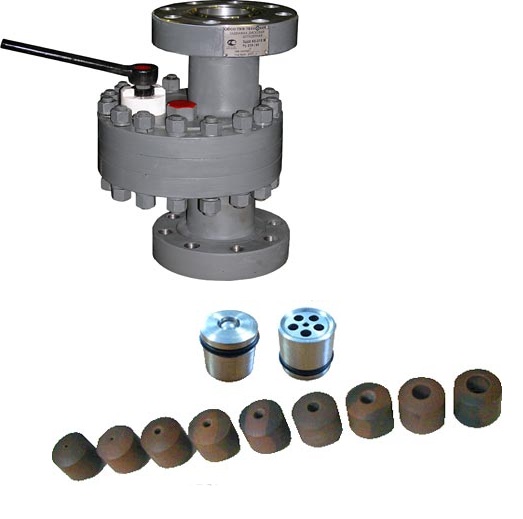
Дисковая штуцерная задвижка (Рис.7) также предназначена для ступенчатого регулирования расхода жидкости или газа за счет совмещения дроссельной втулки (штуцера) с осью трубопровода, но в отличие от револьверной дисковой задвижки, дроссельная втулка выполнена съемной и может быть заменена другой. Замена производится одним оператором в течение 5 минут при закрытом положении задвижки без сброса давления из системы. Недостатком этой конструкции является перекрытие трубопровода при замене дроссельной втулки, что хотя и не на долго, останавливает работу рабочей линии скважины. К общим недостаткам всех дисковых задвижек следует отнести то, что корпус задвижки имеет плоскую форму и патрубки с седлами расположены не концентрично диаметру расположения шпилек крепления полукорпусов, что не рационально с точки зрения жесткости конструкции и может привести к тому, что при деформациях корпуса под действием давления рабочей среды уплотнительные поверхности седел могут перекашиваться относительно плоскости диска и, в следствие этого, возможна потеря герметичности.
Шаровые краны, как наиболее современный и прогрессивный вид трубопроводной арматуры, не могли остаться в стороне от задач регулирования режима работы скважины.
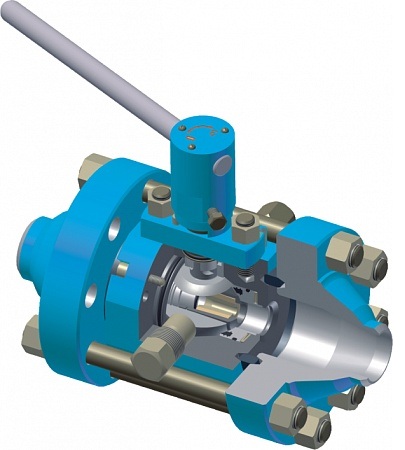
Так сегодня для этих целей применяется шаровые краны со встроенными в шаровой пробке сменными дроссельными втулками (Рис.8). Такой кран позволяет произвести замену дроссельной втулки в течение 5 минут без сброса давления с трубопровода при этом имеется возможность закрыть кран с обеспечением класса герметичности «А» по ГОСТ 9544-2005. Недостатком у этой конструкции, как и у дисковой револьверной задвижки, остается необходимость при замене дроссельной втулки, хотя и не долго, перекрывать трубопровод.
Большое разнообразие конструкций применяемых для регулирования работы скважины говорит о том, что оптимальное решение еще не найдено. Имея в наборе всю выше перечисленную разношерстную технику у изобретателя Власова В.А. и его коллег из ООО «НПЦ ОСТА» возникла идея «запрячь параллельно в трубопровод» несколько шаровых кранов и таким образом решить проблемы автоматизации процесса регулирования.
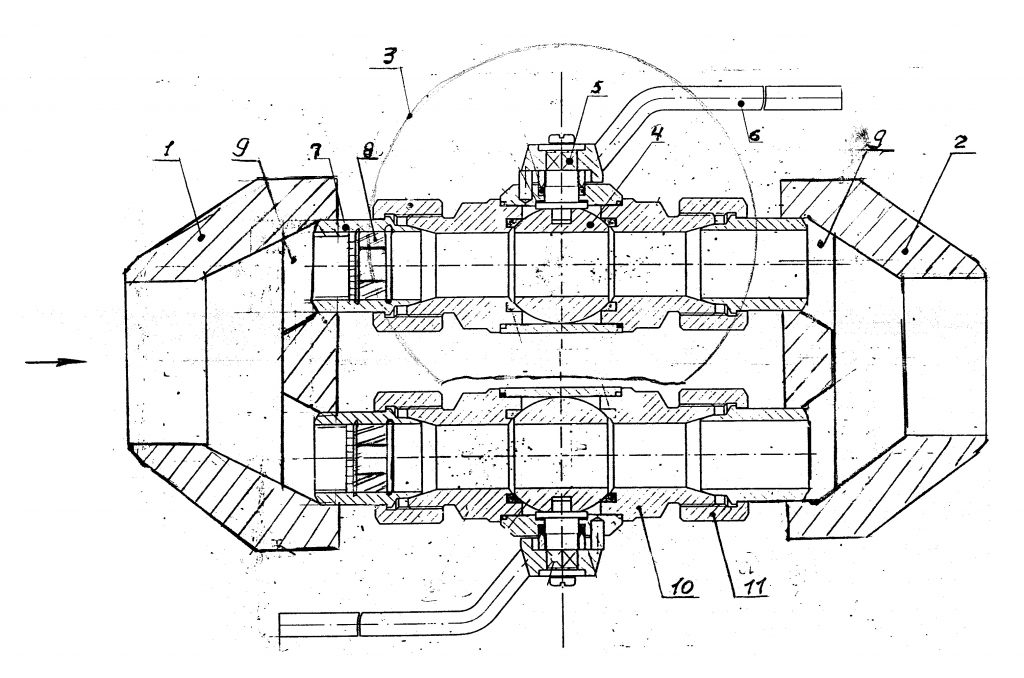
Автором с 2006 года было получено ряд патентов, в том числе патент № 94729 на
полезную модель «Задвижка регулятор расхода жидкости или газа многоканальная на высокое давление для интенсификации нефтедобычи» (Рис.9). Отличительной особенностью полезной модели является то, что между фланцами установлены два обычных шаровых крана, а дроссельные втулки установлены в ниппелях шаровых кранов. По информации автора «первые модели регуляторов (около 40 единиц) успешно эксплуатируются на Приобском, Омбинском, Мало-Балыкском, Мамонтовском и.др. месторождениях ООО «РН-Юганскнефтегаз». Ведущие нефтегазодобывающие предприятия, такие какОАО «Тюменнефтегаз», ОАО «Нижневартовское НП», ООО «Газпромнефть Ноябрьск-нефтегаз» используют с 2007 года по 10 единиц регуляторов. При этом «Ноябрьск-нефтегаз» эксплуатирует регуляторы на давление 32 Мпа. Производство, поставку, гарантию осуществляет ООО «Лениногорский опытный завод нефтеавтоматики» (ЛОЗНА)» [4]. В дальнейшем мысль изобретателя перешла от двух шаровых кранов к четырем шаровым затворам, установленным в одном общем корпусе. Автором был получен патент №77461 на полезную модель «Регулятор расхода жидкости или газа межфланцевый на высокое давление» (Рис.10). Отличительной особенностью этой полезной модели является то, что корпус выполнен цельным в виде межфланцевого кольца с четырьмя каналами, причем с одного торца корпуса в каналы устанавливаются шаровые пробки, а с другого торца корпуса – дроссельные втулки. Как пишет автор, однокорпусные регуляторы отличаются от ранних моделей «кратным уменьшением габаритов, массы, себестоимости. Автором получены положительные отзывы — акты применения. Задвижки-регуляторы кардинально отличаются от известных прототипов наличием нескольких (например, четырех) параллельных затворов (в том числе шарового типа) с индивидуальными приводами. Стоимость задвижек-регуляторов доведена ниже уровня стоимости задвижек типа: ЗДШ, ЗДШМр, ЗМС, ЗМШ, КШД.» [4].
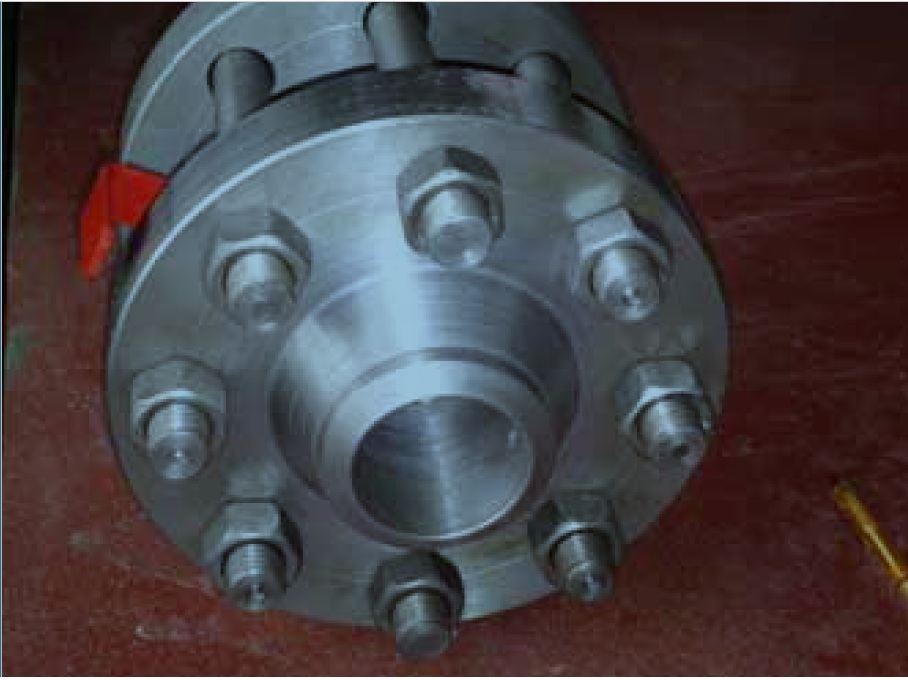
Необходимо отметить, что конструкция с параллельным расположением шаровых затворов является рациональным и логичным шагом в развитии регуляторов для фонтанной арматуры. Один шаровой кран не смог эффективно решить стоящие перед ним задачи, поэтому складывание положительных свойств отдельных единиц позволило получить дополнительно новые свойства. Однако факт отсутствия широкого внедрения этой конструкции на промыслах заставляет задуматься о причинах мешающих ее признанию.
И так, в предлагаемой конструкции используются такие общеизвестные в арматуростроении детали как шаровая пробка, седла, шпиндель, керамические втулки, что с уверенностью позволяет гарантировать доступность ее изготовления на предприятиях, специализирующихся на выпуске шаровых кранов и работоспособность изделия в реальных условиях. Оригинальным решением является объединение перечисленных деталей в единой конструкции с возможностью выполнения задач по ступенчатому регулированию расхода рабочей среды. Как известно сопротивление шарового крана в открытом положении близко к сопротивлению прямой трубы такого же диаметра. Отсутствие выступающих частей в проходе запирающей пробке крана гарантирует длительную его работоспособность в открытом положении даже при сильно абразивной среде и надежную герметичность в положении крана «закрыто». Использование в конструкции задвижки-регулятора нескольких шаровых кранов, для ступенчатого регулирования расхода рабочей среды путем их поочередного закрытия, предполагает значительно больший ресурс работы по сравнению с традиционными конструкциями угловых регулирующих дросселей. К недостаткам конструкции следует отнести то, что в случае выхода из строя деталей одного из кранов необходим демонтаж устройства целиком, это же относится и к работам связанным с заменой изношенных дроссельных втулок. Для проведения этой операции, как и в случае с простым дросселем, необходимо работу скважины переводить на запасной отвод, на котором должен быть установлен резервный дроссель заданного диаметра, затем сбрасывать давление с линии и только после этого разбирать фланцевое соединение и демонтировать регулятор с трубопровода, таким образом, смена дроссельной втулки регулятора все так же трудоемка и длительна.
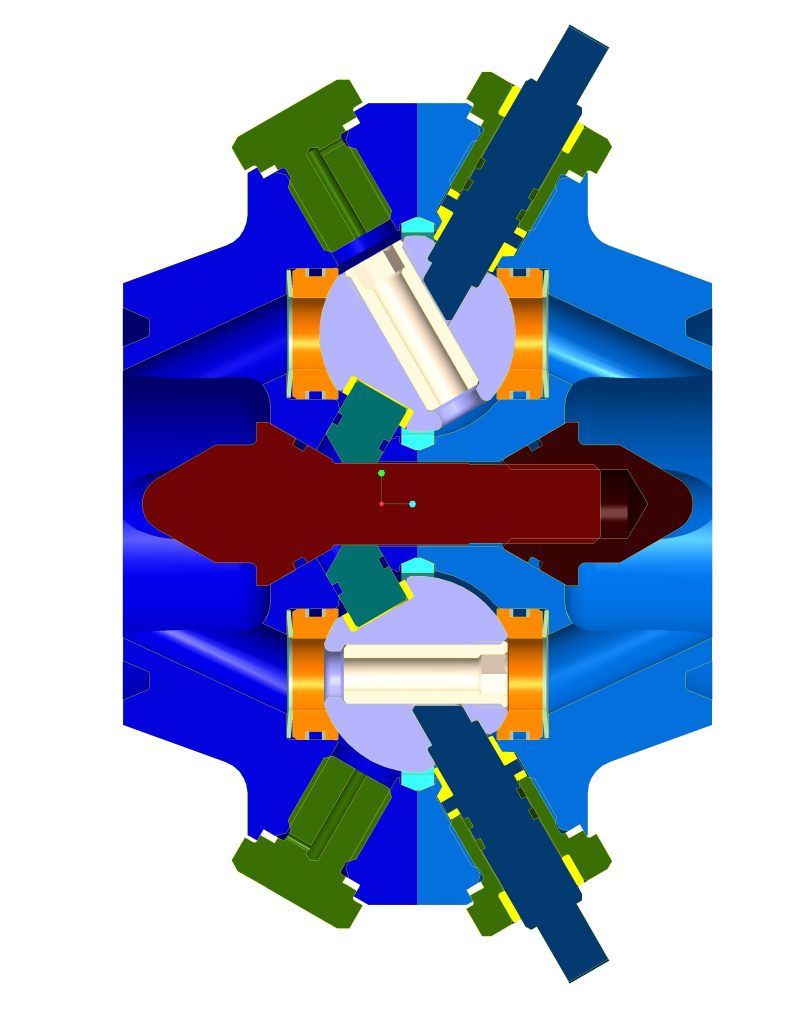
Видя принципиально удачную идею, но и недостатки в ее реализации, автором статьи было принято решение поднять конструкцию на новый уровень развития, устранив ее слабые места. Первым делом было решено применить разборной корпус, состоящий из двух одинаковых полукорпусов (Рис. 11). Полукорпуса стягиваются между собой центральным болтом, так как конструкция регулятора межфланцевая, то центральный болт разгружен, а работают шпильки фланцевого соединения. Решение выполнить корпус с центральным разъемом позволило уйти от конструкции кранов с «плавающей пробкой» и перейти к конструкции — «пробка в опорах». Учитывая большие значения давления рабочей среды (до 35МПа), это решение позволило снизить момент на шпинделе крана и, как следствие, при автоматизации регулятора применить для управления менее мощные и более дешевые привода. Снижение момента на шпинделе позволило также перейти от уплотнения крана «полимерными седлами» к уплотнению — «металл по металлу». Такое решение в условиях абразивных и агрессивных сред позволило резко повысить ресурс шаровых затворов. Кроме этого в каждом шаровом затворе ось шпинделя и ось проходного отверстия в пробке выполнены не перпендикулярными друг к другу, также ось шпинделя не перпендикулярна и к оси седел. Это необычное решение позволило в проходном отверстии шаровой пробки установить сменную дроссельную втулку и обеспечить возможность ее замены на работающем трубопроводе без его остановки. Как и в обычном шаровом кране в положении «открыто» отверстие в шаровой пробке совпадает с каналом в корпусе. Для закрытия крана необходимо пробку повернуть на угол 90˚, при повороте пробки на угол 180˚- отверстие в шаровой пробке с установленной дроссельной втулкой совпадает с технологическим отверстием во втором полукорпусе, что позволяет произвести демонтаж дроссельной втулки. Для этого выкручивается травмобезопасная заглушка, через отверстие в которой, с полости между седлами сбрасывается давление, в результате чего седла плотно прижимаются к поверхности шаровой пробки, обеспечивая тем самым надежную герметизацию полости. В результате сброса давления появляется возможность извлечь дроссельную втулку с шаровой пробки и на ее место установить другую. Все это делается без остановки трубопровода, пока меняется дроссельная втулка на одном кране – работают параллельно расположенные другие краны.
Новый регулятор может работать по следующему алгоритму, например, когда в скважине давление высокое – используется только один кран со вставкой небольшого диаметра. По мере снижения пластового давления – поочередно дополнительно открывается 2-й, 3-й, 4-й краны со вставками небольшого диаметра. Если давление падает настолько, что суммарного диаметра отверстий во втулках не хватает – при закрытом положении каждого крана демонтируется соответствующая дроссельная втулка и на ее место устанавливается дроссельная втулка с отверстием большего диаметра. В случае выхода из строя втулки в результате эррозионного износа, всегда имеется возможность произвести ее замену на новую без остановки трубопровода. В итоге, получаем ремонтопригодную многоступенчатую систему регулирования расхода как путем перекрытия кранов, так и путем замены втулок, что позволяет сократить затраты времени на изменение режима работы скважины и при этом не требуется дополнительного перекрытия трубопровода и использования специального инструмента.
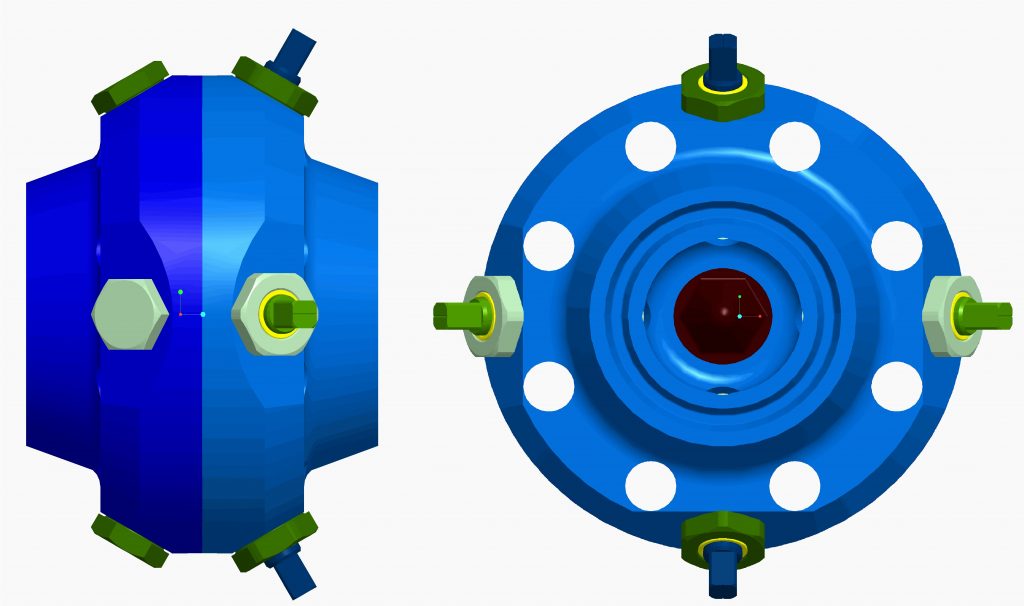
Рассматривая новый регулятор (Рис.12), первоначально складывается впечатление, что он сложнее и дороже традиционных конструкций в виду наличия четырех шаровых узлов, но более детальное изучение преимуществ показывают его эффективность за счет повышения надежности и упрощения обслуживания. К основными достоинствами нового регулятора следует отнести:
— компактность;
— ремонтопригодность;
— возможность производить быстрое ступенчатое регулирование расхода рабочей среды;
— благодаря установке в шаровые затворы дроссельных втулок с разным диаметром отверстий возможно за счет поочередного или одновременного открытия затворов добиться точного регулирование в течение длительного времени без переналадки;
— возможность производить замену четырех дроссельных втулок под давлением через отверстия в корпусе;
— в момент замены дроссельных втулок по трубе продолжает подаваться рабочая среда, так как имеется возможность использовать резервные затворы;
— в отличие от регулируемого дросселя в конструкции отсутствуют линейно перемещающиеся детали, что исключает выход из строя в результате отложения в его полостях песка или замерзания воды;
— конструкция может быть автоматизирована и включена в систему САУ при установке на каждый затвор приводов.
— предполагается значительный экономический эффект в результате снижения потерь материальных и финансовых ресурсов из-за простоев скважин.
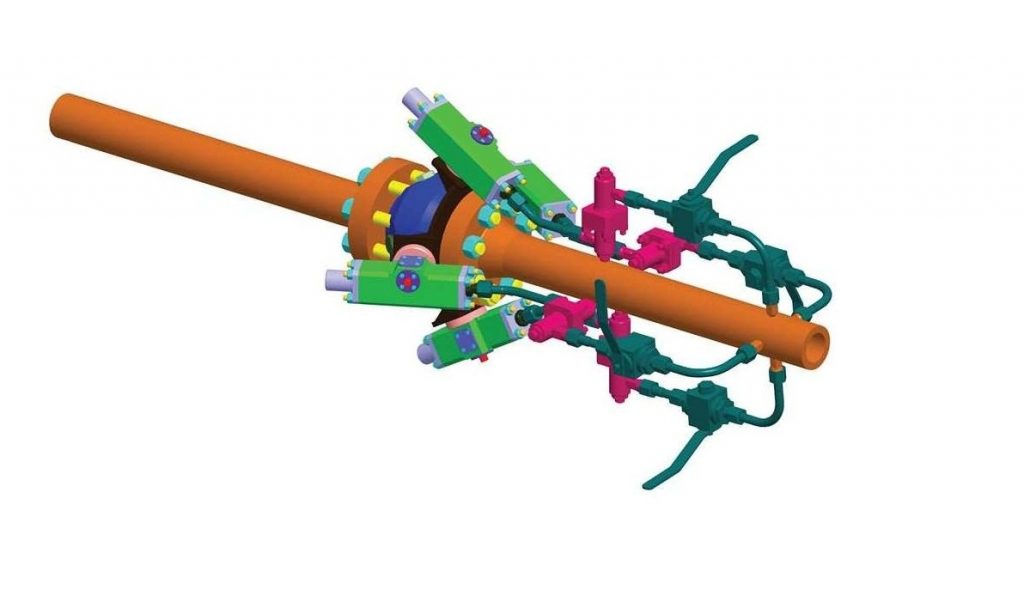
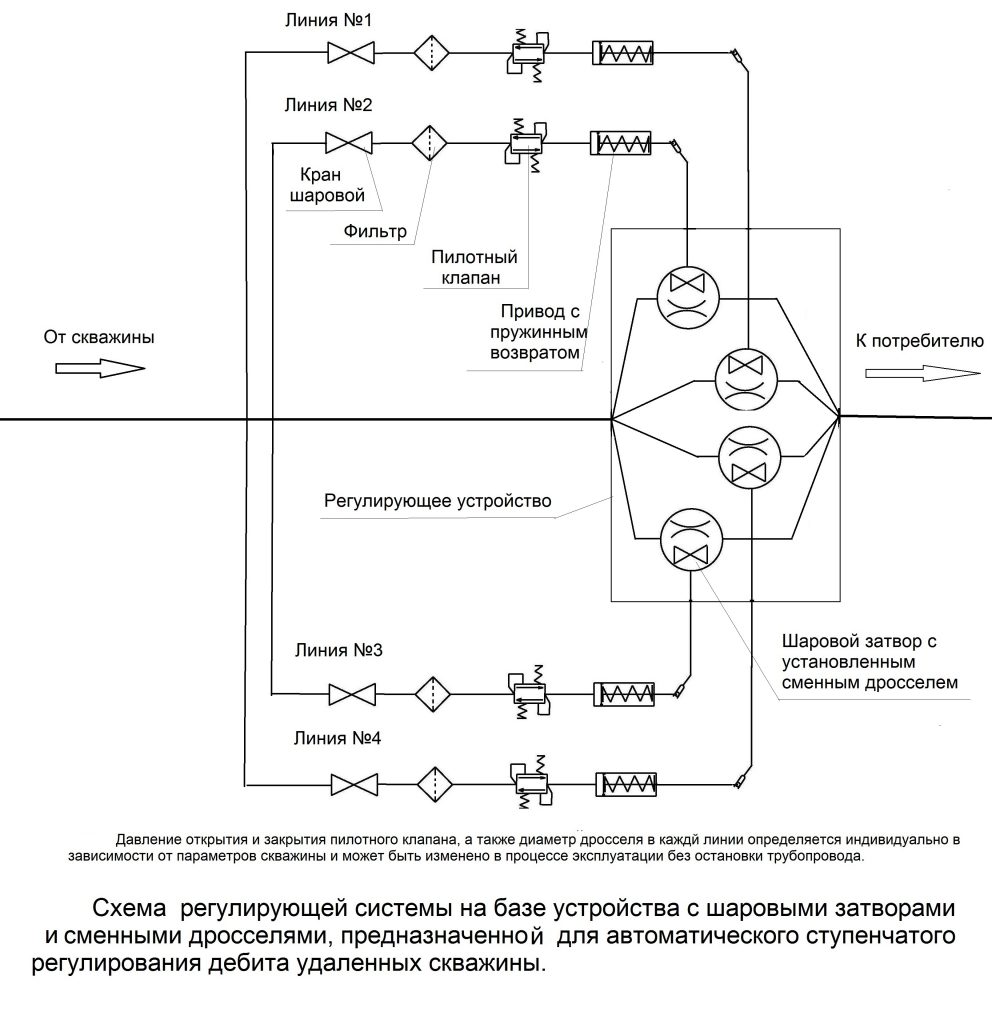
Новый регулятор может быть применен в системе автоматизированного регулирования дебита удаленных или находящихся в труднодоступных местах скважин, где обслуживание и присутствие персонала затруднено или где отсутствует энергоснабжение. Ниже приведено внешний вид (Рис. 13) и принципиальная схема (Рис. 14) системы автоматического регулирования «до себя» на базе нового регулятора (система может быть построена на регулирование «после себя»). Принцип работы заключается в том, что при повышении давления рабочей среды в трубопроводе и достижении установленного значения срабатывает пилот «на подачу», после этого рабочая среда через фильтр попадает в цилиндр привода, в результате поршень перемещается, сжимая пружину и шаровой затвор закрывается. Когда давление в трубопроводе начинает снижаться, пилот закрывается, в результате давление в цилиндре привода сохраняется на первоначальном уровне, при дальнейшем снижении давления шаровой затвор остается в положении «закрыто» до достижения установленного нижнего предела, после чего срабатывает пилот «на сброс», давление с привода сбрасывается в трубопровод и под действием энергии пружины привод открывает шаровой затвор. Привод должен быть спроектирован на работу на разнице давления между установленным значением срабатывания пилота «на подачу» и установленным значением срабатывания пилота «на сброс».
Таким образом, устанавливая в регулятор дроссельные втулки с разными диаметрами отверстий, а также задавая давление открытия и закрытия пилота, можно смоделировать требуемый режим работы скважины, который будет поддерживаться длительное время без необходимости вмешательства человека и без потребления внешней энергии.
Для проверки предлагаемых технических решений приглашаем заинтересованные стороны к изготовлению и испытаниям опытных образцов нового регулятора, со своей стороны готовы разработать конструкторскую документацию, как на сам регулятор, так и на систему автоматического регулирования под конкретные требования заказчика.
Список литературы:
1. Шульга В.Г. Бухаленко Е.И. Устьевое оборудование нефтяных и газовых скважин. Справочная книга, М.: Недра, 1978, C.6/
2. http://www.korvet-jsc.ru Акционерная компания «Корвет». Каталог. Оборудование для добычи и транспортировки нефти и газа.
3. http://www.technovek.ru Завод нефтегазового оборудования «Техновек». Запорная и запорно-регулирующая арматура. Задвижки для нефтяной и газовой промышленности.
4. http://www.ngv.ru «Нефтегазовая Вертикаль — Технологии» №6 (апрель 2015г.) Валентин Власов, ООО» НПЦ ОСТА» Оптимизация нефтедобычи многозатворными задвижками.
5. Патент № 94729 от 27.05.10 Задвижка регулятор расхода жидкости или газа многоканальная на высокое давление для интенсификации нефтедобычи. Власов В.А., Фериченкова Е.В.
6. Патент №77461 от 10.01.08 Регулятор расхода жидкости или газа межфланцевый на высокое давление. Власов В.А., Фериченкова Е.В., Фериченков А.В.
Опубликовано в журнале «Арматуростроение» №5/2015